The Articulating Wood Snakes
Video Link: https://youtu.be/4gjCOKrucIA
My son’s 6th birthday was coming up, and it seems to be a modern kid’s party tradition for all the attendees to get a gift bag or something. I’ve previously 3d printed up stuff to give to kids, which is easy to do, but has the one drawback of being plastic. Plastic plastic plastic…especially black plastic. Sure, PLA is “recyclable” (will that really happen?) and made from food starches (corn, etc), so it isn’t too bad.
Before I get too deep, you can download the digital files and plans for this project here: Articulating Wood Snake Digital Files. The files and a complete set of directions are free! I was initially going to charge $5 for them, but vastly underestimated people’s desire to make this project. I’ve had one free download of it so far.
So, I set out to design a toy for the kids that wasn’t plastic. The goals:
- Wood
- Moves
- Animal
I was heavily inspired by the 3d printed toys that are designed with joints to be “print in place”. These articulating little things are really amazing feats of design. Now, the joint design is based on how a 3d printer works, layer by layer where it is hard to do overhanging parts. For a wood toy, I figured I could go to a ball and socket design. Initially I was seeing out some metal or pre-made ball and sockets, but I couldn’t find anything that would meet my design needs, so I figured I could make them out of wood.
I began by doing some CAD work in Fusion 360 to work out tolerances and movements for a wood joint. My idea was simple: cut two halves and glue them together, where one joint would encapsulate the the ball of another.
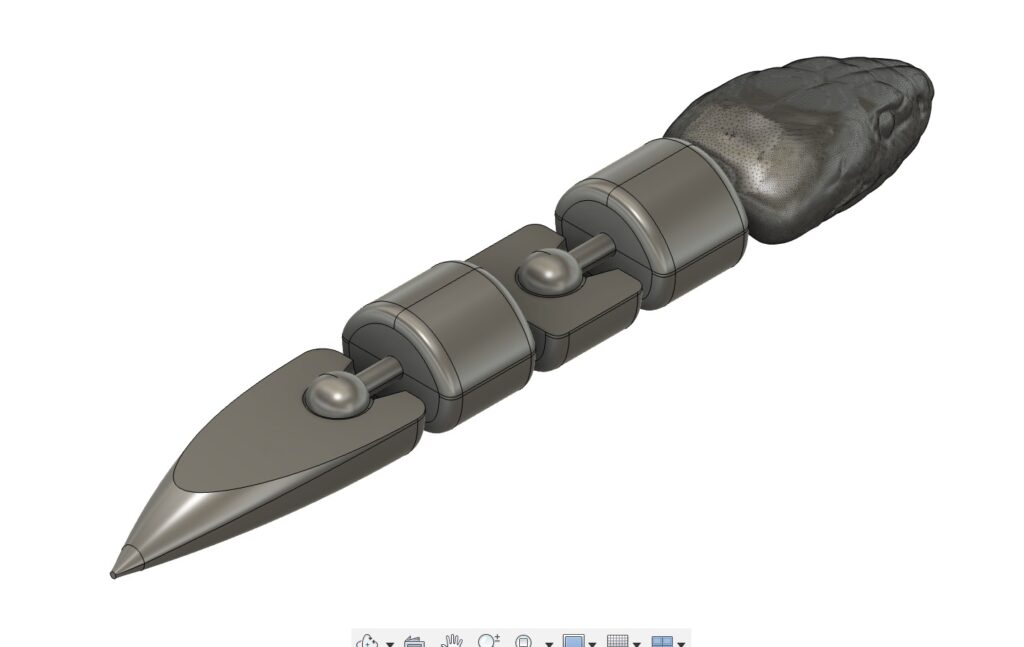
I didn’t take any pictures, but the first test was just a few joints and allowed 360 degrees of rotation. I felt like the complete rotation wasn’t quite “snake like”, so I sought after a way to limit the motion. I settled on making the ball slightly oblong, like a squished sphere or ellipse rotated about the z-axis. I also worked on the shape of the body, making it somewhat flat on the bottom and slightly round on the top. More like how a snake might look laying on the ground with gravity pulling it down.
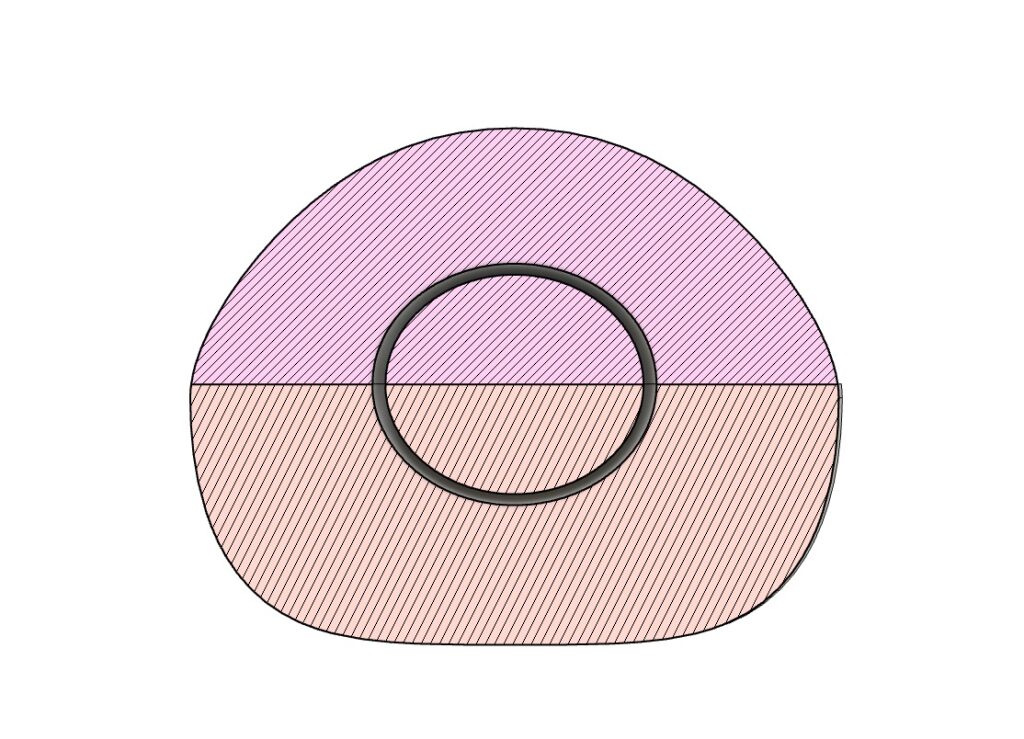
The squished sphere did a good job of limiting the movement, and works almost too well. The wood joints are incredibly strong when made out of a hardwood, but you can except a lot of twisting force and eventually twist the joint to failure, snapping at the shaft. This wasn’t possible when you could rotate the joint 360; there was no pressure points. You also can’t pull the joint out; the wood is super strong lengthwise with the grain. I ended up doing a few tests to get the spacing right before I started production of the snakes.
The snake head is a mesh re-mix from the original 3D printed snake. I took the STL and imported it into Rhino for manipulation. I also exported the ball-and-shaft from my Fusion CAD Design so I could bring it into Rhino. I then combined the shapes into one, but the head was a little blocky. I then exported that shape as an STL from Rhino and opened it into Blender. In Blender I could use the sculpting tools to soften out the mesh. So yeah, three separate programs to do this. Fusion is terrible (and slow) at mesh manipulations, so I couldn’t do it there. Blender is terrible and mesh booleans, whereas Rhino is a lot better. But Rhino doesn’t do sculpting, so I had to use Blender to do that! Finally, Fusion is the only place to do the CAM (I’ll ignore Vectric VCarve/Aspire because I don’t like it’s toolpath generation).
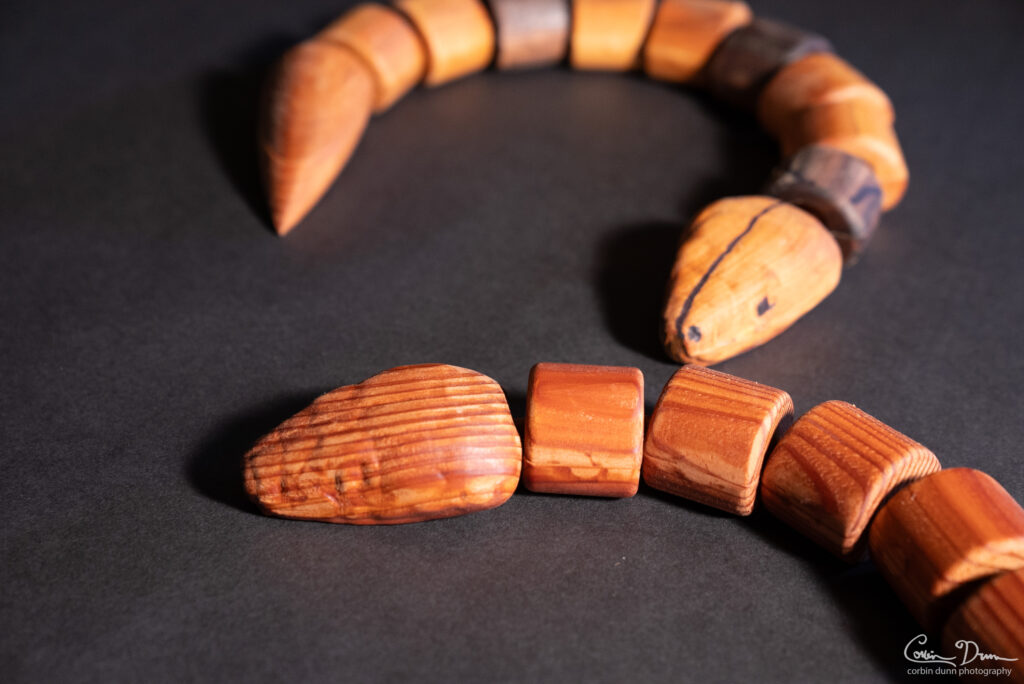
For wood, any hardwood would work well, and I used scraps of cherry and walnut that I had around. I also had a lot of redwood, so I made three out of redwood. This was a mistake, as redwood is just too soft, and the joints quickly failed on one of them. The hardwood joints that Ansel has is still holding up after a month of play, but he also realizes that they can break if he twists them and avoids doing that. Since they are a kid’s toy, I finished them with “Walrus Oil” (brand) Cutting Board Oil, which is a mixture of various food safe oils and bees wax.
I ended up making seven of these snakes. From concept to getting them all done took about a full week off work. I was constantly running the CNC machine to cut all the pieces to get them done in time for his party.