Making a “Waterfall Box” with Epoxy
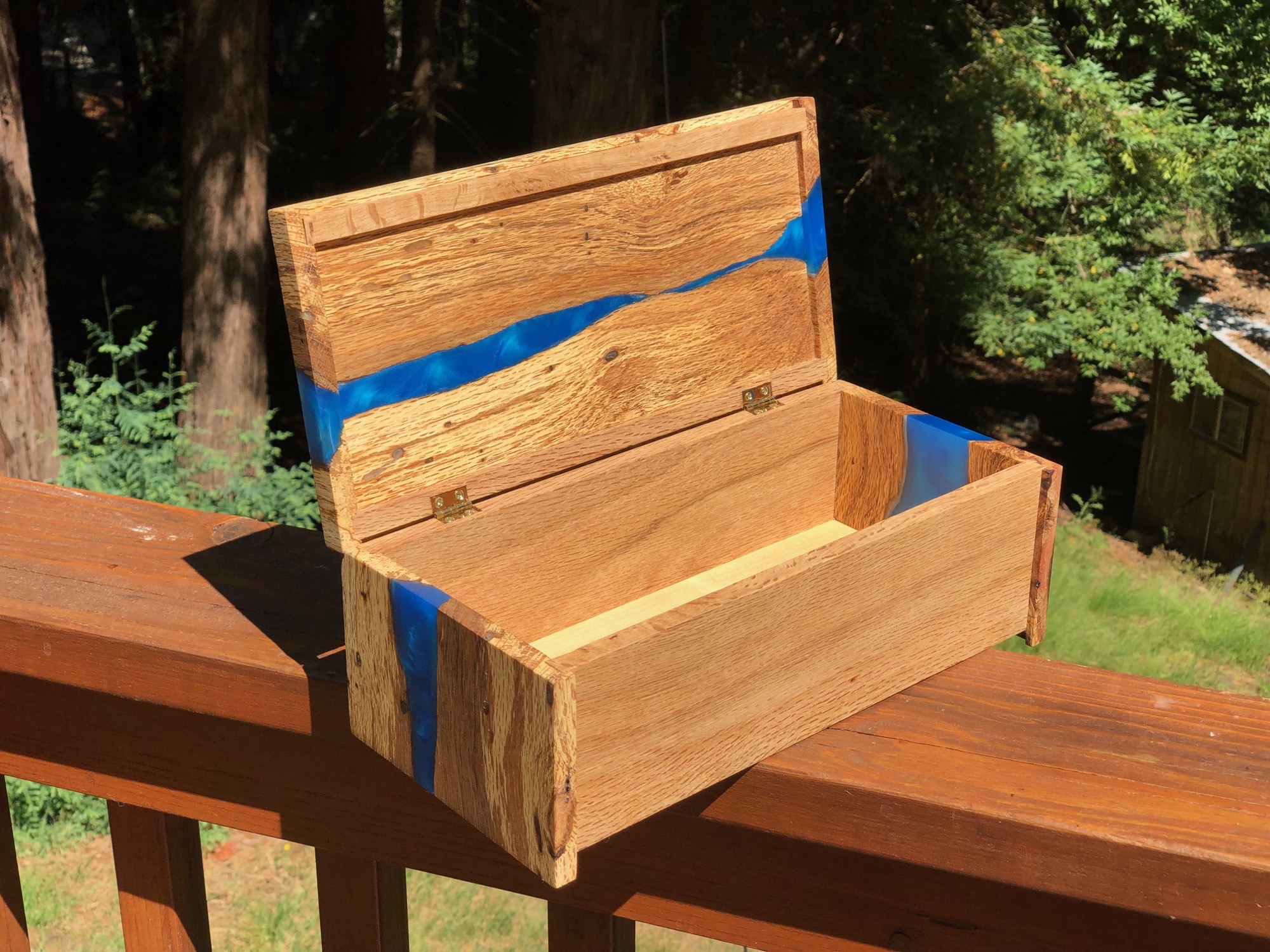
I recently posted a bunch of pictures about my latest “Waterfall River Box”. Here are a few behind the scenes pictures on how I made this box.
First off, this box is for sale over at the Redwood Monkey Workshop: Spalted Oak Blue Waterfall Box.
The wood for this box came from my property and a neighbor’s property where some trees had fallen down. I milled them with my chainsaw and an Alaskan Mill style attachment. The wood had to be carefully dried. I set it up in my garage with stickers and let it air dry for over a year. Even after that time, some of the wood seemed too wet and green. Later I ended up building a small kiln to further dry the slabs.
I wanted to create a waterfall style box with some of the scrap pieces I had around. I used some of my scrap melamine to create a form, and covered it with some tuck tape. The tape is really slick, and doesn’t allow the epoxy to stick to it. I’ve tried not using the tuck tape, and found that the epoxy would still stick to the melamine.
The first step in epoxy work is to seal the wood. I used some “quick coat” epoxy from Stone Coat Countertops. It sets up pretty quickly, and allows me to do a few coats in one day. I applied the epoxy to the bottom and used it to sort of “glue down” the piece to the form. This helps prevent the main river epoxy pour from slipping underneath the form and lifting the wood up. I hadn’t tried this technique before, and it did work great! Not shown is a few moments later when I clamped the pieces down to ensure they were flat on the bottom. I applied two coats of the epoxy along the live edge. This is required to properly seal it; otherwise, the main epoxy pour will get some bubbles seeping into it as air escapes from the wood.
I sanded the sealing coats after they dried in order to allow the main pour to stick to it. I used “Casting Epoxy” from Stone Coat, which can be poured in up to 1” depths. Shallower is fine, but will take longer to dry. The is a 1/2″ depth pour, and would require over 24 hours to dry before I could demoed it. I wanted about 1.5 days, and that seemed like a good time. I would simply test my scrap pour to see how it was setting up and felt hard enough.
The problem with the slow setting epoxy is that any pigment you use will settle to the bottom and give you a murky appearance:
I wanted a cool swirl effect. Every 45 minutes after the pour I would come back down and swirl the epoxy. I did this for up to about 4 hours (at about 68F, higher temperatures will cure faster), and at that point it was getting late and the swirls seemed to hold shape. I would test my leftover bit in the pour bucket to make sure it wasn’t too sticky before I actually swirled my piece:
After I demanded the piece I ran it though my planer. The planer seems to chip out the epoxy a bit, so I only knock off the really high parts, and then sand it off with 60 grit and a random orbital sander. At that point I had a nice piece of wood to work with, and I cut some 45s to generate the waterfall:
I decided to use biscuits to hold the 45s together. 00 size are just small enough to work, but I later realized I shouldn’t put them through the epoxy parts, as the resin is semi-transparent and you can see them close to the surface. This photo below shows my general setup for how I did the joints: biscuits on the 45s, side grooves for the long side pieces, and grooves for the box bottom. The side pieces are also oak, but it isn’t spalted.
The box was amazingly strong when I did some test fittings without glue.
After test fitting, I sanded the interior up to 220, and the exterior up to 150. I save the final sanding for after the box is glued together, in order to knock off any defects that came along from handling. The top was cut off on the tablesaw. I don’t have any photos of the process, but it is fairly easy to do. I first make the long (lengthwise) cuts, but make sure they don’t go all the way through. I keep it off by about 1/16 or 1/32 of an inch. I then raise the blade a bit more and cut the sides all the way through. This keeps the box lid from collapsing into the saw when you cut it free. I then can take a sharp utility knife and cut it free. A few swipes with a hand bland and some sandpaper finish the piece off.
Before final sanding, I routed out some hinge slots and did a test fitting of the lid.
After sanding to 220 I applied Osmo oil, in clear satin. I have been experimenting with various finishes, and I like the Osmo oil the best (so far). I’m also going to try a “conversion varnish” to see how it holds up for tabletops.
That’s it! This box is available for purchase, and I’m asking $120. It has a lot more time and materials in it than some of my other pieces, and I think it is worth a lot more. I’m just trying to charge a fair price.
You might want to post this on Reddit in r/woodworking
Good idea! I can check out that area; I tried reddit a few times to post stuff (such as in unicycling), but I never had enough experience points. The irony of the system is that it is hard to get the points needed to post stuff to certain groups, and it is pointless to post junk to other groups that you don’t like. So, I never really got into using reddit.
[…] wedding. This is the second box I’ve made in this style, with the first one being called a “waterfall box“. I originally started thinking about how I could create a flowing river on the top of a box, […]
[…] out a few pictures of me making this box on my blog post: Making a Waterfall Box with Epoxy and some larger images at: Spalted Oak Blue River […]